I thought I'd share an update on how our little family is doing. Laurie, her sister, and I are all living in a "new" 43 year old house in the Portland area. Initially, after our wedding, Laurie and I were living in her old apartment with her sister while the house was being remodeled.
We are all living in the new house now. We shifted living/sleeping locations soon after the contractor finished remodeling, after a few other little changes were made, and then Laurie finished the huge job of emptying her old 3 bedroom apartment that she and her sister had occupied for a few decades.
Our contractor had a plumber in for the bathroom work, who we asked to look at our low water flow problem. Throughout the entire house, we had a water flow problem. With no flow, the pressure was quite high, 80 PSI, but when any tap was opened the pressure dropped to something like 15-20 PSI, and the flow was maybe 2 gallons per minute. Running the kitchen faucet while someone was in the shower upstairs pretty much turned the shower into a dribble. This wasn’t really a livable situation yet.We knew that the shutoff gate valve just outside the house didn’t fully close, and there was a fair chance that it had failed to fully open as well. The plumber replaced that, which let us finish the interior plumbing work with the water fully shut off. It didn’t improve the flow problem, though.
The plumber had mentioned that many homes had pressure regulator “bell valves” on the water line, often buried. If one of these had failed, essentially stuck slightly open, it could cause this problem. We started a hunt for the valve. It would be either by the shutoff at the house, or by the meter at the street. After a good bit of digging we found it at the meter, about 18” down, buried in the dirt.

We had that replaced, but again, there was no improvement. By then the contractor was done with the remodel, so we thanked and paid him. Laurie decided to excavate the line herself to see if we could find some clue as to the problem. As she dug out from the house, she found the copper pipe transition to old PVC plastic line about 5’ out. Additional digging uncovered a 90 degree bend straight down, and about 3 feet down, another elbow and the line headed more or less toward the meter. With the mess of pipe elbows at the street, we had a pretty twisty water line, although not enough to explain the whole low flow problem. With another 30 feet of three foot trench to dig, we thought it was time to call in the pros.
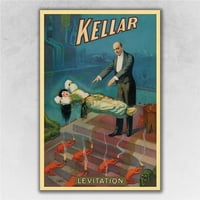
Cornel’s Plumbing agreed to come out and take a look. Alex, the plumber, suggested starting at the meter, opening up the line and checking the flow capacity, and then moving to the house and checking other points until the area with the restriction was found. He rigged a fitting onto the end of the meter, attaching a 50 foot hose. Opening up the meter valve, we had well over 10 gallons per minute out of the hose. Now we knew the problem was on our side of the meter, and not on the city side.
We knew at this point that the flow was poor at the connection to the house, and Alex the plumber had an idea. He took the other end of the hose up to the house, and screwed it onto the hose bib just past the house shutoff valve. Opening the hose valve and street shutoff valve, we had great water flow in the house’s plumbing. He said this lash up with the hose was how they normally supplied water while running a new water line in, but this was only the second time he had seen a home water line blocked in 7 years as a journeyman plumber. The hose lash up told us the water line from the street to the house was where the clog was.
The cost to dig up the old PVC line and find where it was plugged would be high, labor intensive as hand digging was needed to avoid destroying the pipe. It would be much cheaper to put in a new line, better materials, using modern boring technology. We concurred, and he gave us a quote that was much lower than I had expected from doing a little shopping around. So, we bought the replacement installation project.
The crew showed up on time, and went to work. They dove into the crawl space through the hatch in our pantry, scoped out what they needed to do, and started prep. The driller showed up around 11 AM, and set up by the water meter at the street. They started drilling into the gentle slope there, at about the depth of the water line, aiming to miss the other utility lines and tunnel under the house. The plan was to surface the drill head near the pantry crawl space hatch, and install the house shutoff and reducer there, rather than in a vault outside. This would be both more convenient, and avoid any possible frozen pipe issues in the winter. One worker walked along with a special instrument that read out the drill head position, and called out steering instructions to the drill operator. They ran the line over 3 feet deep, past the perimeter foundation, and hit their target. The plumbing crew attached a long length of extremely heavy-duty modern PEX line, and a grounding wire (per code), and this was pulled back through with the drill head. By noon the drill crew was packing up and leaving, and by 2 PM we had a completed new water line in service.
We were ready to move in. With some assistance from a medical supplier, we set up everything for Laurie’s sister, and got her room ready. We would be sleeping in the guest room with my furniture until we got Laurie’s stuff moved from her apartment. We spent a few weeks shifting accommodations, moving boxes and such, and settling in. We thought we had everything in great shape, what with the new roof, new floors, plumbing overhauled, lights working, and a new washer and dryer on the way. We would have a great Christmas in our new home.
Woman plans, Goddess laughs...
The 42 year old Jen-Aire cooktop had other plans. The grill and one burner control failed, and I had the choice of repair or replace in front of me. Replace? There are two downdraft 30” cooktops on the market, and both needed 40 Amp service. We had 30 Amp service installed, which meant that we would have to pull a larger line and install larger breakers. But, the power panel was a Fedeal Electric, which has it’s own issues. Local code would require us to replace the entire panel. The cost of replacing the cooktop was going to be well over $5,000, which wasn’t in the budget.
So, repair. Naturally, the original parts were discontinued about 35 years ago, but there was a suggested replacement. DIscontinued about 20 years ago... The parts are something called an “infinite switch”, the heat regulator for an electric range element. There are so-called “universal” replacements, but they didn’t consider the “unique” wiring of this old cooktop. The cooktop circuitry assumed that the switch internals worked in a certain way, which no modern switch actually does any more, for good reasons. They used their assumption to power up the vent fan whenever the grill was on, bypassing the fan switch. The new switches were wired differently, and resulted in the fan power momentarily being interrupted every few seconds while the grill was on. Even better, if the fan were switched on directly the grill ran at full power, with no temperature control!
Chasing down the internal design of the switches and the wiring of the grill I determined that I needed to disconnect one wire between the fan and the grill proper, and replace the fan switch with a proper double-pole single throw switch, along with the previous replacement of the “infinite switches.” It’s all working now, and the cooktop now largely uses standard parts I can get off the shelf. The fixed cost about $110. While Christmas dinner was cooked entirely in the oven, for New Years Eve we had our cooktop and grill, suitable for some T-bone steaks. Yay!
We’re still slowly unpacking and getting set up. I’m starting to work on proper radio antennas, and Laurie is weeding the backyard using a come-along and some rope rated to 5,600 lbs force (she broke one of her old ropes pulling blackberry vines). Life goes on, and we are enjoying our new home in the “woods.”